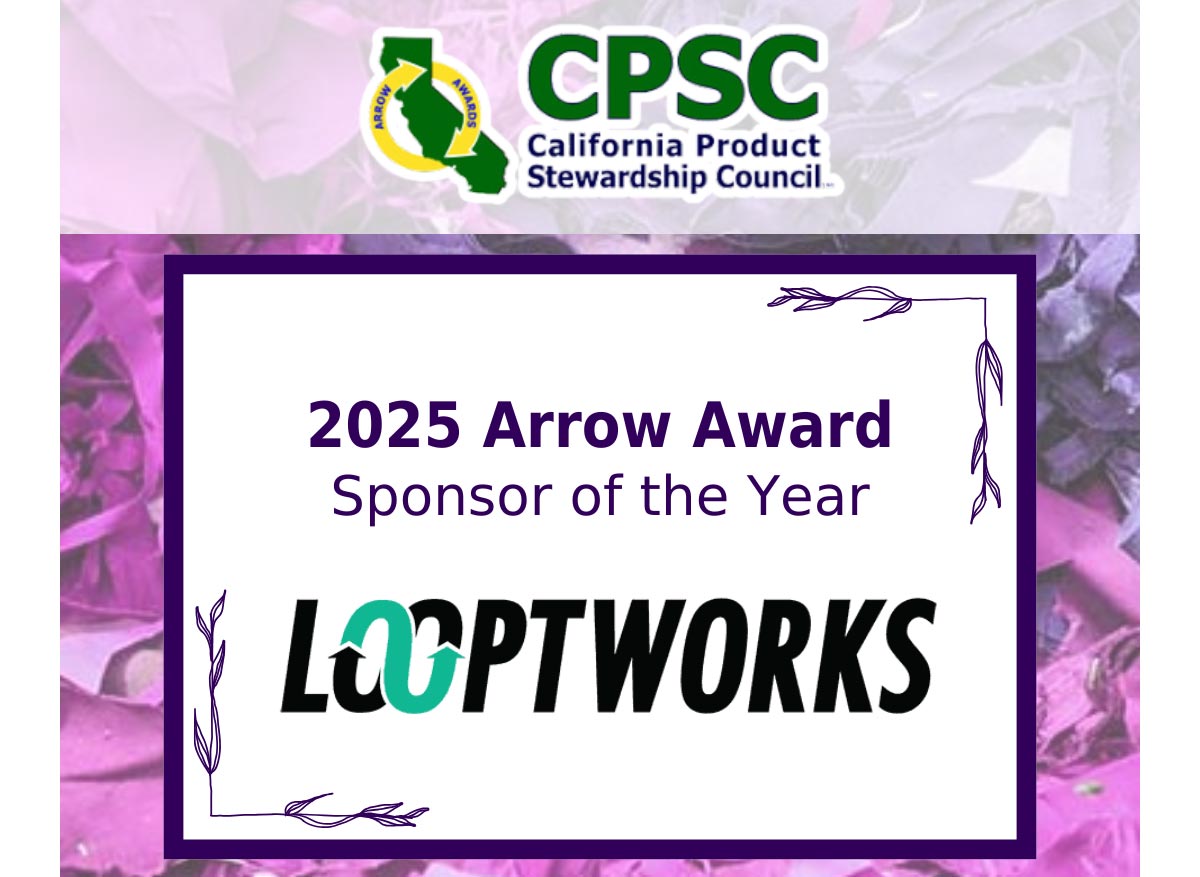
Just over a year ago, we shut down its direct-to-consumer website, where we sold bags and other travel accessories made from upcycled materials, from airplane seats to NBA uniforms, to focus solely on our textile circularity initiative. Today, we’re weeks away from kicking off operations—starting with vertical downcycling—at our 90,000-square-foot state-of-the-art facility in Gresham, Oregon.
As we continue to build out our facility to offer automated sorting and deconstruction along with advanced fiber-to-fiber recycling, we are working to ensure that our space lives up to who we are as a brand. Through innovation, responsibility, and authenticity, Looptworks strives to use only what already exists. For example, we’re repurposing hard utility lines and heating our space with waste energy. Read on to learn more about the sustainability features that are helping bring our energy-efficient facility to life.
Oregonians may be familiar with the old R.R. Donnelly building, the home of a Yellow Pages printing press facility. After phone books died off, the space was vacant for many years and was eventually used as a storage warehouse. Now, Looptworks is breathing new life into the building, reconstituting it back into a manufacturing environment.
Bringing a 40+-year-old building up to code compliance is not an easy feat. For example, we’ve had to rebuild all of our hard utilities, from gas meters and electricity to phone lines and internet, as parts of the building degraded over time and must be modified for our purposes. At the same time, the project has challenged us to find ways to use the old building’s systems in new and different ways.
“We’re trying to do as much as we can to repurpose, recycle, and bring circularity into everything,” said David Dean, Looptworks’ lead mechanical engineer. “We’ve reused electrical fittings, electrical wiring, electrical conduits, junction boxes, isolation switches, air lines, air valves, air filters, and water lines all to make sure we throw away as little as possible and we recycle and repurpose as much as possible.”
In short, we’re putting some very modern systems inside a very old shell. But because the building is as old as it is, it’s extremely well-built. “Some modern buildings are not built with a 100-year lifespan in mind,” said Dean. “Back when this building was built in the late 1970s, it was. There are many decades left of the fabric of this building.”
Energy efficiency is the name of the game at our new facility. That means using waste, solar, and thermal energy and displacing the need for hydrocarbons or grid energy.
We are working closely with the Energy Trust of Oregon to implement energy-efficient lighting, manufacturing equipment, and the star of the show—a proprietary HVAC system that uses pressure differentials to heat and cool the building, reducing our need for gas and offering enormous energy savings.
How exactly does it work?
Our recycling processes generate a lot of air, and that air is quite warm. In the winter, we can use it to comfortably heat our 90,000-square-foot facility. In the summer, we will use vents repurposed from the building’s original HVAC system to pull air out of the building, creating negative pressure inside the facility. That negative pressure will then draw ambient air in from outside, resulting in the flow of cool air throughout the facility.
The energy-efficient heating-and-cooling system is a custom pilot project with the Energy Trust of Oregon that relies heavily on data gathering, algorithms, and high-tech measuring devices. For example, thermostats and air pressure gauges feed data into the system so that it knows when to open vents or change the direction of airflow in the building. The Energy Trust has lent us all the equipment we need to optimize our process so that similar HVAC systems may soon be rolled out in other facilities.
“We anticipate that we will go down to a zero, or as near to zero as we can get, usage of natural gas,” said Dean. “Right now, the building has freeze protection for the wintertime and that’s a natural gas system. But we hope to eliminate the use of that.”
As our new facility comes online, we will harvest solar energy to power everything other than our high-ampage manufacturing equipment. This includes office functions and the EV chargers in our parking lot. We’ll also use solar energy to power electric forklifts, allowing us to move away from using propane.
We can’t forget about the S in ESG—social impact. Through the City of Gresham’s WorkSource program, we connect with diverse community groups, from local colleges to women’s shelters. Our goal is to offer employment opportunities and on-the-job training to underserved groups. Over the next few months, we will increase our hiring efforts, as our initial textile recycling processes will require manual sorting of garments. This is an easily teachable skill that will allow us to partner with local community members as we work to keep millions of pounds of textile waste out of landfills.
Reach out to our solutions team today to explore what a partnership with Looptworks could look like for your company.
We’d love to hear from you!
Denine has over 20 years of experience driving new business opportunities for leading companies, including E.I. DuPont de Nemours & Company, Inc., The Dow Chemical Company, Outlast Technologies, and DST Systems. She holds a BS from the University of Pittsburgh and a Certification in Executive Management from the Kenan-Flagler School of Business at the University of North Carolina at Chapel Hill.
Tami is a senior accounting leader with over 16 years of experience in the manufacturing and textile industry. Her specialties include process development and implementation, mergers and acquisitions, job and project costing and analysis, and managing complex teams and technical projects. Tami has served as Chief Financial Officer and Controller for a variety of innovative companies, where her analytical skills and strategic mindset helped organizations create efficiencies in their financial systems.
Kelley is a passionate and strategically minded business development leader with more than two decades of experience in the sporting goods apparel industry. He has experience in product construction, league partnerships, retail relationships, supply chain management, sustainability, circularity, and carbon footprint management. Kelley builds successful partnerships by putting the customer first while simultaneously advancing his organization’s business objectives.
Suzy is a product leader and operations expert with more than 25 years of experience in the textile industry. She is passionate about finding creative solutions to complex problems and motivating people to action through vision, strategy, collaboration, and communication. Suzy has proven expertise in product development, sustainability, marketing, supply chains, and innovating processes and best practices to drive results.
Scott is a visionary leader with more than 32 years of experience in strategic branding, innovative product creation, supply chain sustainability, and sales and marketing for global organizations. He founded Looptworks in 2009 as an industry solution for turning excess materials into upcycled consumer products. In 2022, Scott transitioned the company to a B2B business model focused on eliminating global textile waste through closed-loop solutions.
Scott is a visionary leader with more than 32 years of experience in strategic branding, innovative product creation, supply chain sustainability, and sales and marketing for global organizations. He founded Looptworks in 2009 as an industry solution for turning excess materials into upcycled consumer products. In 2022, Scott transitioned the company to a B2B business model focused on eliminating global textile waste through closed-loop solutions.